 |
|
 |
|

Dear Readers,
This is the first of a series of quarterly reviews on selected topics of electrical/electronic connector technology.
You are invited to suggest a review topic of interest.
Roland S. Timsit, President Timron Scientific Consulting Inc. Tel: 416-787-8161,
www.timron-inc.com
Also in this newsletter: 2001 Conferences on Electrical/Electronic Interconnections
and Electronic Packaging.
|
 |

Electrical Connector Lubricants
Lubricants (solid and liquid) or sealant greases are often
used to enhance the performance of electrical connectors. Although there is considerable
evidence about the benefits of these materials, there is still debate and confusion
about the range of applications, and the limitations, of lubricants and greases in
electrical connectors.
Let us clarify the technical jargon. In the electrical connector industry, the term
"lubricant" is generally employed only in reference to separable electronic
connectors where maximum power dissipation is relatively low, say 0.1 - 0.5 watt or
less. Separable connectors may operate in a hot environment, sometimes approaching
2000C, as under an automobile engine hood. The major functions of a lubricant
in separable connectors are to reduce friction during installation and minimize mechanical
wear during connector service. There are other expected functions of the lubricant, as we
will see later.
Again as regards technical jargon, the term "sealant grease" is generally used
in reference to permanent electrical connections as in bolted and compression connectors.
In these connector types, maximum power dissipation extends beyond about 0.5 watt,
often reaching several watts or even tens of watts. Such connectors are confined largely
to the transportation, power electronics and power-utility industries. Although the term
"grease" suggests a lubrication function, the major function of a "sealant
grease" is to mitigate ingress of corrosive material into electrical interfaces with
the conductors.
Solid and Liquid Lubricants in Separable Connectors
Lubricants intended for separable connectors come in two forms, solid and liquid. Because
an electrical interface is produced by contact of micro-asperities on the surfaces of
mating bodies, as illustrated in Fig.1, an effective connector lubricant must not
interfere with the formation of electrically-active contact spots (also known as a-spots
[1]). For this reason, a lubricant must be either electrically conductive or, if
non-conductive, it must be easily displaceable from areas of potential a-spot formation.
There are relatively few solid lubricants available to the connector industry.
Despite their excellent lubrication properties, solids such as Mo2S, H3BO3
[2] and multicrystalline waxes are not used in electrical contacts because they are
neither good electrical conductors nor easily displaceable in an interface. On the other
hand, lamellar graphite is often used in power contacts, particularly with electrical
brushes in machinery and electric trains, to take advantage of the unique lubrication and
electrical conductivity properties of that material [3].
Currently, the only widely used solid lubricant in separable electrical connectors is gold
deposited as a thin layer. So-called "hard" gold, consisting of gold alloyed
with a small amount (< 1wt%) of cobalt or nickel, offers acceptable lubrication
properties. The excellent electrical conductivity properties of gold also promote superior
electrical connectibility. The lubrication offered by hard gold is superior to that of
pure gold because unalloyed gold is soft and tends to stick to a mating surface.
This stickiness leads to an increase in friction as illustrated in Fig. 2. Optimal
lubrication with hard gold is achieved for a layer thickness of about 0.1 micrometer [4].
At this layer thickness, the coefficient of friction (COF - the ratio of drag force
to contact force) drops to about 0.3 as illustrated in Fig. 2. Thicker layers lead to
"ploughing", whereby the gold is pushed out to the front and sides of a wear
track during sliding, thus increasing friction. Other materials such as palladium-nickel
and palladium-cobalt are being investigated as solid lubricants in separable connectors
[5].
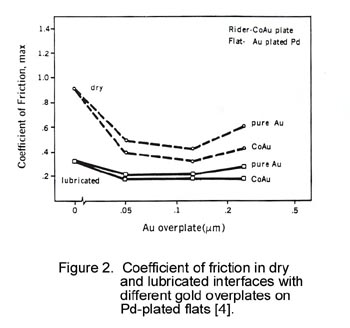
We now consider liquid lubricants. Liquid lubricants usually reduce the COF to the 0.1 -
0.2 range [4]. The COF is relatively independent of lubricant layer thickness so long as
the speed of interfacial displacement remains relatively small (i.e. no larger than
several centimeters per second). This constancy of friction stems from the expulsion of
any significant lubricant accumulation from the contact region, leaving only a
molecularly-thin lubricant film in the interface. This lubrication mechanism is known as
"boundary" lubrication and is illustrated in Fig. 3 [6]. Reduced friction stems
from an inability of the residual lubricant layer in the interface to sustain any
significant shear force during sliding.
Boundary lubrication is sustained only if the bonding energy of lubricant molecules to the rubbing
surfaces is sufficiently large. [7]. If this bonding energy is too small, the lubricant
does not adhere well to the contact surfaces. In this event, lubricant molecules become
incapable of supporting a contact load as illustrated in Fig. 3 and can be easily squeezed
out of the contact interface [8,9]. This mechanical dispersion of molecular lubricant
layers leads to high friction and large adhesive wear during sliding.
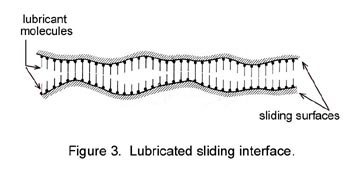
In addition to reducing friction and minimizing mechanical wear, a liquid lubricant
must mitigate fretting corrosion and protect against atmospheric corrosion in contact
areas of a connector. Liquid lubricants are ideally suited to perform these
additional functions due to their ability to be displaced back and forth over contact
areas by random or imposed displacements in a sliding interface. This motion leaves
molecularly-thin deposits between larger lubricant pools, which can lead to substantial
surface coverage [8] and protection against corrosion since lubricant layers (no matter
how thin) block metal oxidation sites. Clearly, the ability of a lubricant to
protect against corrosion relates to the bonding energy of the lubricant with the contact
surfaces. Too small a bonding energy compromises the ability of the lubricant to
stick and undermines its corrosion-inhibiting properties.
One highly desirable property of connector lubricants is the ability to remain
localized near an area of contact and not spread over connector surfaces where the
lubricant is not needed. Although some spreading of the lubricant is desirable to maximize
surface coverage, minimize friction and enhance protection against corrosion,
excessive spreading can be detrimental to connector performance. A full discussion
of wetting and spreading characteristics of lubricants is beyond the scope of this review.
However, the use of connector lubricants such as perfluoroalkylethers was discontinued
because of pervasive unwanted spreading of these liquids [10].
Usually, a liquid lubricant is first diluted in a solvent and then deposited on the
connector contact surfaces. The lubricant remains as a deposit after the solvent has
evaporated. One important properties for an effective lubricant is a low vapor pressure,
and hence a low evaporation rate, over the service temperature range. This insures
survival of the lubricant over the expected life of the connector.
Liquid lubricants owe part of their lubrication properties to the length of the molecular
chain. In general, the longer the length of the lubricant molecule, the farther away the
sliding surfaces are kept apart during sliding. Hence the COF decreases with increasing
lubricant molecular chain length, as illustrated in Fig. 4.
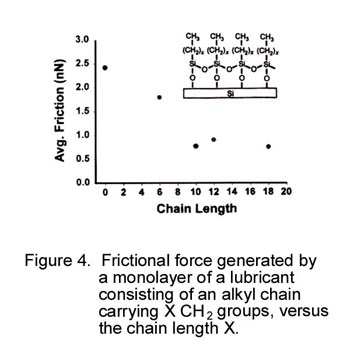
One prerequisite for effective lubricant action in electrical connectors is chemical
inertness towards the metal surfaces to be lubricated. For example, lubricants used on
copper or silver-plated surfaces should not carry sulfur-containing compounds since
these may react with the metals to generate resistive metal sulfide films and increase
contact resistance. Similarly, lubricants used with aluminum connectors (e.g. in
power-utility connections) should not contain carboxylic acid or equivalent additives
(which are excellent lubricants) since these materials react with aluminum to generate
electrically-insulating oxide layers [11].
In recent years, one family of lubricants identified as polyphenyl ethers (PPEs) has been
used successfully in tin-plated, gold-based material systems and other metals in separable
connectors [12]. Some formulations of PPEs have been more successful than others in
minimizing fretting corrosion and increasing resistance to atmospheric corrosion in
separable connectors [13]. The reasons for the effect of PPE chemical structure on
resistance to fretting and atmospheric corrosion [13] are currently unclear. The
elucidation of the relationship of chemical structure to lubricant properties promises to
yield a new generation of lubricants with superior protection properties for separable
connectors, and lower cost.
Connector Greases
Greases are widely used in permanent power connectors deployed by the power-utility, power
electronics and transportation industries. These connectors comprise bolted, compression
and wedge-type devices. In power-utility applications, the connectors are generally
supplied with the grease already applied to the contact surfaces.
Greases are pastes consisting of a thickening agent, one or more lubricant materials and
possibly other chemical compounds such as antioxidants. The thickeners include finely
divided silica, soaps, clays, Teflon powder and various gelling agents usually at 5-10 wt%
concentration. Grease structures generally consist of interlocked fibrous crystallites or
finely divided particles with a large surface area. The solid components of a grease form
a matrix in which lubricants, antioxidants and other additives are entrapped. The COF
provided by greases is generally larger than that produced by liquid lubricants i.e.
0.3-0.5 for greases versus about 0.2 for liquid connector lubricants. This difference
usually stems from the presence of solid materials in the greases.
Greases used in electrical power connections may also contain fine particulate material.
The particulates may comprise a hard abrasive material such as a ceramic or hard metal,
or consist of a relatively soft metal such as zinc or silver. Hard grit material is
used in conjunction with aluminum connections to abrade electrically-insulating aluminum
oxide films on the surfaces of conductors and connectors, and allow the generation of
large areas of metal-to-metal contact. The use of soft metals is designed to penetrate
surface contaminant layers, including tenacious oxide layers, to form
electrically-conducting metal paths across electrical interfaces.
One intended function of a grease in a permanent power connector is to inhibit corrosion
by sealing electrical contact areas from the environment. The grease is introduced as a
filler material to eliminate interstrand gaps within power cables and to fill voids at
electrical interfaces with the connector. In a recent investigation of connector failure
by corrosion in a marine environment [14], it was noted that grease residues left over in
failed connections had not maintained their original paste consistency. The residual
grease became dry, brittle and thoroughly interspersed within the corrosion products. In
contrast, grease residues in connectors that had not failed in the same environment had
kept their paste consistency. These observations point to a proneness of currently-used
connector greases to react chemically with corrosion products. These observations
indicate that greases (i.e. "sealant greases") designed for permanent connectors
are not always capable of preventing the ingress of corrosive contaminants. The
observations also indicate that much work remains to be done for the development of
reliable connector sealant greases.
Conclusions
Recent years have witnessed significant advances in the design of superior solid and
liquid lubricants for separable connectors, and in the formulation of "sealant
greases" for permanent connectors. Many of the advances have been achieved
empirically by trial-and-error. Although this approach has been rewarding, it needs to be
complemented by fundamental work to generate an understanding of selected properties of
lubricants and greases. In the author's view, only the combination of empirical and
fundamental work can accelerate significantly the development of truly innovative
connector lubricant products.
References
- Holm, R., Electric Contacts, Theory and Applications, Springer-Verlag, Berlin,
1976.
- Singer, I.L., "Solid Lubrication Processes", in Fundamentals of Friction:
Macroscopic and Microscopic Processes, Eds. Singer, I.L. and Pollock, H.M., p.237,
NATO ASI Series, Kluwer Academic Publishers, London, 1992.
- Shobert, E.I., "Sliding Electrical Contacts (Graphitic Type Lubrication), in Electrical
Contacts, Principles and Applications, Ed. Slade, P.G., p. 839, Marcel Dekker, Inc.,
New York, 1999.
- Antler, M., "Tribology of Electronic Connectors: Contact Sliding Wear, Fretting,
and Lubrication", in Electrical Contacts, Principles and Applications, Ed.
Slade, P.G., p. 309, Marcel Dekker, Inc., New York, 1999.
- Boguslavsky, I., Abys, J.A. and Eckert, V.E., "Electroplating of PdCo alloy for
connector application", Proc. 29th IICIT Connector and Interconnection Symposium, p.
219, 1996.
- Bowden, F.P. and Tabor, D., The Friction and Lubrication of Solids, Oxford
University Press, London, U.K., 1950.
- Fairlie, M., Pathak, B.R. and Timsit, R.S., "Reflection-absorption IR spectroscopy
of organic monolayers on aluminum surfaces", Proc. 1985 Conf. Fourier Computerized
Infr. Spectrosc., SPIE, vol. 453, p.496, 1985.
- Timsit, R.S. and Pelow, C.V., "Shear Strength and tribological properties of
stearic acid films - Part I: On glass and aluminum-coated glass", ASME J. Tribology,
vol. 114, p. 150, 1992.
- Timsit, R.S. and Pelow, C.V., "Shear Strength and tribological properties of
stearic acid films - Part II: On gold-coated glass", ASME J. Tribology, vol. 114, p.
159, 1992.
- Antler, M., "Sliding studies of new connector contact lubricants", IEEE Trans.
on Components, Hybrids and Manufacturing Technology, vol. CHMT-10, p. 1, 1987.
- Timsit, R.S., Bock, E.M. and Corman, N.E., "Effect of surface reactivity of
lubricants on the properties of aluminum electrical contacts", IEEE Trans. On
Components, Packaging and Manufacturing Technology, Part A, vol. 21, p. 500, 1998.
- Antler, M., "Electronic Connector Contact Lubricants: the Polyether Fluids",
", IEEE Trans. on Components, Hybrids and Manufacturing Technology, vol. CHMT-10, p.
32, 1987.
- Joaquim, M.E., "Connector contact lubrication with polyphenyl ether: a
review", Proc. 30th Annual Connector and Technology Symposium, p. 217, 1997.
- Callen, B.W., Johnson, B., King, P., Abbott, W.H. and Timsit, R.S., "Environmental
degradation of utility power connectors in a harsh environment", IEEE Trans. CPT,
vol. 23, p. 261, 2000.

2001 Conferences and Workshops on Electrical/Electronic Interconnections and Electronic Packaging
- High Speed Digital Interconnects, 14 - 16 January 2001, Radisson Resort and Spa
Scottsdale, Scottsdale, AZ, [ www.iwpc.org ].
- IEEE 14th International Conference on Micro Electro Mechanical Systems, 21 - 25 January,
Casino Kursaal Interlaken, Interlaken, Switzerland, [ www.ieee.org
].
- Annual Reliability and Maintainability Symposium (RAMS), 22 - 25 January, Philadelphia
Marriott, Philadelphia, PA, [ www.rams.org ].
- The 2001 European Systems Packaging Workshop, 22 - 24 January 2001, Sitges, Spain, [ www.ieee.org ].
- Microtech 2001, 28 - 31January 2001, Novotel, West London, England, U.K., [ www.imaps.org ].
- 2001 IEEE Power Engineering Society Winter Meeting, 28 January - 01 February, Hyatt
Regency Columbus, Columbus, OH, [ www.ieee.org ].
- 2001 IEEE Burn-in and Test Sockets Workshop, 4 - 7 March, Hilton Mesa Pavilion, Mesa,
AZ, [ www.bitsworkshop.org ].
- International Symposium and Exhibition on Advanced Packaging Materials, 11 - 14 March
2001, Chateau Elan, Braselton, GA, [ www.imaps.org ].
- Ceramic Technologies for Microwaves, 26 - 27 March 2001, Adams Mark Hotel, Denver, CO, [
www.imaps.org ].
- International Conference and Exhibition on High Density Interconnect and Systems
Packaging, 17 - 20 April 2001, Santa Clara Convention Center, Santa Clara, CA, [ www.hd-international.com ].
- 2001 International Conference on Electronic Packaging (and 15th Electronic Show), 18 -
20 April, Tokyo Ryutsu Center, Tokyo, Japan, [ www.imaps.org
].
- Advanced Technology Workshop on Thermal Management for High -Performance Computing and
Wireless Applications, 20 - 21 April 2001, Sheraton Palo Alto Hotel, Palo Alto, CA, [ www.imaps.org ].
- 2001 IEEE International Reliability Physics Symposium, 30 April - 3 May, Wyndham Palace,
Orlando, FL, [ www.irps.org ].
- IEEE MTT-S Ceramic Packaging Workshop, 20 - 25 May 2001, Phoenix, AZ, [ www.imaps.org ].
- 2001 IEEE 51st Electronic Components and Technology Conference (ECTC 2001), 29 May - 1
June, Buena Vista Palace, Orlando, FL, [ www.ieee.org ].
- 13th Microelectronic and Packaging Conference, 30 May - 1 June 2001, Strasbourg, France,
[ www.imaps.org ].
- 2001 IEEE International Interconnect Technology Conference, 3 - 6 June, Hyatt Regency
Hotel, Burlingame, CA, [ www.his.com/~iitc ].
- Topical Workshop and Exhibition on Flip Chip Technology, 18 - 20 June 2001, Four Seasons
Hotel, Austin, TX, [ www.imaps.org ].
- 2001 8th International Symposium on Physical and Failure Analysis of Ics (IPFA 2001), 9
- 13 July, Westin Stamford and Westin Plaza Hotel, Singapore, [ www.ewh.ieee.org/reg/10/ipfa/ ].
- 2001 IEEE Holm Conference on Electrical Contacts, 10 - 12 September, Hotel Wyndham
Montreal, Montreal, Canada, [ www.ewh.ieee.org/soc/cpmt/tc1/2001call.html
].
- 34th Annual Connector & Interconnection Technology Symposium & Trade Show, 1 - 3
October 2001, Disneyland Hotel and Conference Center, Anaheim, CA, [ www.iicit.org ].
- 34th International Symposium on Microelectronics, 9 - 11 October 2001, Baltimore, MD, [ www.imaps.org ].
- 2001 IEEE/PES Transmission and Distribution Conference and Exposition, 28 October - 2
November, Georgia World Congress Center, Atlanta. GA, [ www.ieeet-d.org
].
- Behaviour of Electrical Equipment and Components in Tropical Environments, 3 7
September, Radisson Plaza Hotel, Cairns, Australia,
[ www.cigre.org/GB/IMEETINGS/fsIM.htm
].
|
 |
|
 |
|
 |
|